Plastic extrusion for complex profiles and custom designs
Plastic extrusion for complex profiles and custom designs
Blog Article
Trick Benefits and Considerations of Implementing Plastic Extrusion in Your Jobs

Understanding the Basics of Plastic Extrusion
Plastic extrusion, a staple in the production market, is a process that involves melting raw plastic product and reshaping it into a continuous profile. This profile, once cooled, can be cut into desired lengths or coiled for later usage. The elegance of plastic extrusion exists in its flexibility. A wide variety of products, from piping to window structures, can be created. The procedure calls for an extruder, an intricate device with a heated barrel, a turning screw, and a die at the end. The plastic material, in the kind of pellets, is fed into the extruder, where it's melted and required through the die, taking its shape. The choice of plastic and the layout of the die identify the item's qualities.

The Economic Advantage of Plastic Extrusion
The economic benefit of plastic extrusion exists mainly in two areas: cost-efficient product manufacturing and useful manufacturing speeds. With plastic extrusion, organizations can produce high volumes of material at a reduced price compared to other approaches. The process flaunts a remarkable manufacturing rate, considerably decreasing time and further enhancing its financial viability.
Cost-Effective Product Manufacturing
A significant benefit of plastic extrusion is its remarkable cost-effectiveness. This manufacturing procedure permits continual, high-volume manufacturing with marginal waste, which translates into lower expenses. The raw materials made use of, normally plastic pellets, are relatively affordable contrasted to other compounds (plastic extrusion). The procedure itself requires much less energy than lots of various other manufacturing approaches, even more reducing costs. In addition, the extrusion procedure enables for a high degree of precision fit the plastic, minimizing the need for costly post-production alterations or corrections. The longevity and longevity of extruded plastic items commonly suggest less require for substitutes, adding to long-term cost savings. All these elements make plastic extrusion a highly affordable choice for many tasks, using an attractive balance between cost and efficiency.
Beneficial Production Speeds
While preserving the cost-effectiveness of the products, an additional noteworthy advantage of plastic extrusion depends on its fast production rates. This performance in the manufacturing process is attributed to the constant nature of the extrusion process, permitting high-volume manufacturing in a relatively brief time span. The speed of production straight correlates to a reduction in labor costs and a rise in result, thus improving the overall economic stability of the process. The busy production does not endanger the top quality of the last item, guaranteeing dependable and consistent results. This mix of quality, speed, and cost-effectiveness emphasizes the considerable financial benefit of applying plastic extrusion in various tasks.
Convenience and Personalization: The Staminas of Plastic Extrusion
One of the famous staminas of plastic extrusion depends on its flexibility and personalization possibility. These qualities open up the door to endless design possibilities, offering producers the capacity to tailor items to certain requirements. This heightened level of personalization not just enhances item capability however likewise considerably increases product individuality.
Unrestricted Style Opportunities
Plastic extrusion radiates in its ability to offer practically endless layout opportunities. This technique provides liberty to create intricate accounts and intricate forms, an accomplishment tough to accomplish with other manufacture techniques. Owing to the fluid nature of molten plastic, the procedure is adaptable enough to generate a varied series of measurements, types, and sizes. The plastic can be adjusted to match one-of-a-kind specifications, enabling the production of personalized geometries and meeting certain customer demands. Plastic extrusion can take care of a range of plastic types, broadening its application extent. This versatile method, as a result, serves a wide variety of sectors from construction to automotive, packaging to electronics, and past. With plastic extrusion, the layout possibilities are virtually endless.
Boosting Item Originality
The versatility of plastic extrusion can significantly enhance product uniqueness. This process enables designers to experiment with different shapes, sizes, and colors, providing the freedom to create special items that attract attention on the market. It is this customization that lends a distinct identification to each item, differentiating it these details from its rivals.
Along with its visual benefits, the customizability of plastic extrusion also provides practical advantages. Developers can modify the buildings of the plastic according to the details demands of the application, improving the item's functionality. As an example, they can make the plastic extra flexible, a lot more durable, or much more immune to warm, depending upon what the product requires. Therefore, plastic extrusion not just boosts item originality yet likewise its utility and marketability.
Layout Limitations in Plastic Extrusion: What You Required to Know
Exactly how can design restrictions potentially influence the procedure of plastic extrusion? While plastic extrusion is flexible, layout restrictions can stop its advantages. Recognizing these restrictions is vital for effective implementation of plastic extrusion in your jobs.
Assessing the Environmental Impact of Plastic Extrusion
While understanding style constraints is a substantial facet of plastic extrusion, it is similarly important to consider its ecological ramifications. The process of plastic extrusion includes melting plastic materials, potentially releasing hazardous gases right into the environment. Using recycled plastic products in the extrusion process can decrease ecological influence.
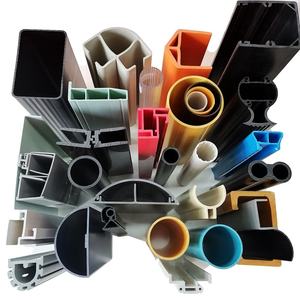
Situation Research: Successful Projects Utilizing Plastic Extrusion
Success tales in the area of plastic extrusion abound, demonstrating both the adaptability and efficiency of this manufacturing procedure. plastic extrusion. One more effective case is the production of plastic film for packaging and farming. These circumstances illustrate plastic extrusion's crucial function in various fields, confirming to its versatility, cost-effectiveness, and dependable result.
Conclusion
In conclusion, plastic extrusion provides a effective and economical approach for generating complicated forms with minimal waste. While it provides various advantages such as cost-effectiveness and flexibility, it's critical to think about possible style restrictions and environmental effects. Implementing recycled or biodegradable products can alleviate these concerns, enhancing sustainability. Including plastic extrusion into projects can bring check here about effective outcomes, as confirmed by countless study.
Plastic extrusion, a staple in the production market, is a process that involves melting raw plastic product and reshaping it into a continuous profile. Plastic he has a good point extrusion can manage a selection of plastic types, increasing its application extent.Exactly how can design restrictions possibly affect the process of plastic extrusion? The process of plastic extrusion involves melting plastic materials, potentially releasing unsafe gases into the environment. Utilizing recycled plastic products in the extrusion procedure can lower environmental effect.
Report this page